Sigma Phase Embrittlement-Refractory Anchor Failure
- matintegrity
- Jan 28, 2023
- 4 min read
Sigma phase embrittlement phenomena is the formation of a metallurgical phase known as "Sigma Phase" in some stainless steels when they are heated above about 1000 °F (540 °C) that can result in a loss of ductility and fracture toughness and can lead to cracking failure. This type of embrittlement can occur in a variety of industries, including nuclear power, aerospace, and petrochemical, and can have serious consequences for the safety and reliability of structures and equipment.
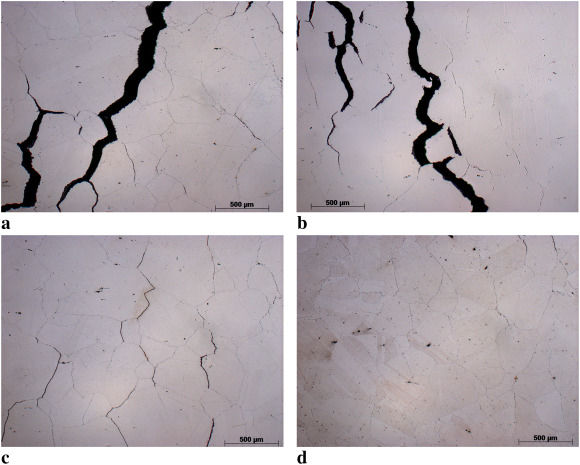
The factors that affect sigma phase formation are the alloy composition, temperature, and exposure time. The formation rate increases with increasing chromium and molybdenum content. Stainless steels with sigma phase can normally withstand operating stresses at operating temperatures but upon cooling below about 500 °F may show a complete lack of fracture toughness. Therefore formation of sigma phase in austenitic stainless steel weld metals can occur in a few hours. The tensile strength and yield strength of sigmatized stainless steels increases slightly compared with solution annealed material. This increase in strength is accompanied by a reduction in ductility and a slight increase in hardness.
To prevent sigma phase embrittlement, it is important to understand the conditions that lead to its formation and to carefully control the thermal and mechanical processing of austenitic SS.
Uncovering the Root Cause of Refractory Anchor Failure in a Power Plant
The failure of refractory in boiler applications is a common occurrence, with the failure of anchor rods being the main cause. This failure can be caused by defects in the weld such as improper use of weld consumables, non-standard weld procedures or practices, formation of deleterious phases (Sigma phase) in the weld, cracks in the weld zone caused during welding, lack of fusion, and lack of penetration of weld. Improper material selection in terms of high temperature strength and corrosion resistance to service environment is also a reason for anchor failure.
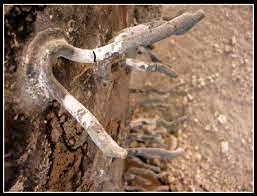
In this specific case, the base material selection was correct but the chemical composition of the failed anchor fell short of the range specified for chromium, nickel, and manganese levels. The presence of Sigma-Phase, a hard intermetallic phase. This phase reduces toughness, creep and fatigue strength. The failure was caused by thermal exposure in the Sigma-Phase formation range, frequent thermal load disruptions due to shutdowns caused shock loading of the anchor and thus Sigma-Phase embrittlement induced cracking occurred leading to lesser support for the refractory.
The failed section consisted of 800x600x120mm panels of castable refractory with backup insulation of 280mm and metallic anchors of AISI309 SS grade welded to mild steel (MS) plate, for reinforcement. Service temperature at the hot face area was 800oC (max.). The service period for the anchors was 3 years, during which there were 35 shutdowns. Of these, 17 were within the 4 months preceding the failure.
More frequent shutdowns and shock loading will result in brittle failure of component material in presence of Sigma phase.
The investigation revealed that the anchors had straightened instead of maintaining their curved shape and had oxidation, elongation and erosion features on the surface. The plant also reported buckling of the outer shell at the failed location with damage to the backup insulation.

Chemical analysis of the failed and unexposed anchors was conducted and the results showed that the chromium (Cr), nickel (Ni) and manganese (Mn) levels were lower and silicon (Si) was marginally higher than the specified range for AISI-309 SS. Hardness, tensile strength and metallography analysis were also conducted on the anchors. The results revealed that the hardness level of the failed anchor rod was higher compared to the unexposed anchor rod. The metallography analysis revealed the presence of sigma phase in the failed anchor and grain boundary cracks in the coarse grained HAZ adjacent to the weld.
the investigation revealed that the failure of the refractory panel and anchors can be attributed to a poor quality of the weld with Sigma-phase formation and microcracks along the grain boundaries, as well as inadequate expansion joint which allowed flue gas to enter and damage the backup insulation. These factors, along with the decrease in strength at high temperatures, resulted in buckling of the outer shell and failure of the anchors at the weldment. The Sigma-phase formation at the non-welded end of the anchor rod also contributed to the weakening of the refractory reinforcement and ultimately led to the failure of the refractory panel.
How could we prevent similar failure or formation of Sigma Phase Embrittlement - Prevention Tips:
Take the necessary precautions to avoid applying high stresses to sigmatized materials during a shutdown to prevent brittle fractures.
300 series SS materials can be de-sigmatized by solution annealing at 1950 °F (1065 °C) for 4 hr followed by a water quench.
To minimize sigma phase in welds, control the ferrite content by specifying the allowable range of ferrite in the weld metal (e.g. 5-9% for Type 347, less for Type 304) and limiting the maximum ferrite content to minimize sigma formation during service or fabrication.
Ensure a minimum ferrite content to minimize hot short cracking during welding, can be measure by ferrite content measuring instrument.
How could we detect before a catastrophic failure - Detection Tips:
Although this damage mechanism is very difficult to find and is also time dependent. (may take a while to develop in service), the following detection techniques can be utilized for early detection.
Using Infrared thermography can help detect the hot spots during operation, hot spots reveals damaged refractory.
Thorough visual inspection during shutdowns and turnarounds should follow focusing on hot spot areas.
Have you found this useful for your plant
Yes
No
I need more information in this case
I need advice on other case
Read the full case in below link:
Komentari