Caustic SCC-Real Case of Pressure Vessel Catastrophic Failure
- matintegrity
- Jan 2, 2023
- 3 min read
Caustic stress corrosion cracking is a form of cracking mechanism that occurs when a material is subjected to the combined action of tensile stress and corrosion caused by specific caustic conditions on a material. The tensile stress can be caused by external loads or internal stresses within the material (applied or residual stresses), and the caustic conditions are typically provided by a corrosive environment such as an aqueous solution of sodium hydroxide or potassium hydroxide.
Caustic SCC is characterized by surface-initiated cracks which sometimes described as a spider web of small cracks that often initiate at or interconnect with weld-related flaws that serve as local stress risers. This cracking mechanism occur in piping and equipment exposed to caustic (alkaline hydroxide solutions) at elevated temperature This type of cracking is particularly common in materials such as Carbon steel, low-alloy steels, 300 series SS and other alloys containing elements such as nickel and chromium are susceptible, it also can be a major problem in industries such as refinery, chemical processing, power generation, and water treatment.
The susceptibility of these materials can depend on a variety of factors, including their chemical composition, microstructure, and the specific operating conditions to which they are subjected.
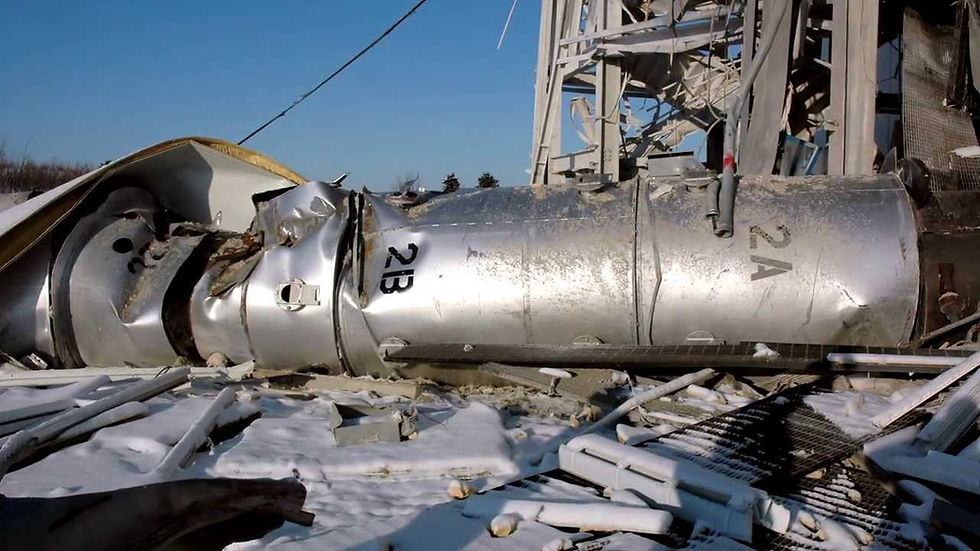
Photo Credit: https://i.ytimg.com/vi/uo7H_ILs1qc/maxresdefault.jpg
Typically materials that are highly corrosion-resistant are less likely to be affected by caustic stress corrosion cracking. This can include materials such as certain grades of stainless steel and certain nickel-based alloys. However, even these materials can be susceptible to caustic stress corrosion cracking if they are subjected to sufficiently high levels of operating parameters (temperature & pressure), tensile stresses and corrosive conditions.
The first factor is tensile stresses that can generate from external sources (such as applied loads or thermal stress from use) or from residual stresses from manufacturing processes (such as welding, bending, or forming). In particular, residual welding stresses (stress that remains in the metal after welding) can be very high and may exceed applied stresses, making the metal more susceptible to cracking.
Note for most designs following common codes, the applied stresses are not high enough to cause cracking due to caustic substances. To reduce the risk of cracking, stress relief heat treatments (including post-weld heat treatment) can be used to alleviate residual stresses.
The second factor that can contribute to caustic stress corrosion cracking is operating under corrosive environments such as aqueous solutions of sodium hydroxide or potassium hydroxide. These solutions can attack the surface of the steel and create small cracks or defects that can then be propagated further up to failure or rupture.
Preventing caustic stress corrosion cracking of process equipment requires a combination of corrosion prevention measures and stress management. This can include the use of:
Corrosion-resistant CRA materials,
Protective coatings,
Corrosion inhibitors,
Stress-relieving techniques such as shot peening or heat treatment.
Properly design the vessel fulfilling construction code requirements to minimize stress concentrations and ensure that it is not subjected to excessive loads and stresses.
The third factor is high or elevated operating temperature and high pressure, both can have a substantial effect on caustic stress corrosion cracking. In general, high temperature can increase the susceptibility of a material to corrosion as high temperature can increase the rate of corrosion and the rate at which cracks propagate. This is because higher temperatures can increase the solubility of corrosive species in the environment, leading to more aggressive corrosion. In the other hand, high operating pressure can increase the tensile stresses on the material.
It is important to consider the effect of high temperature and high pressure on caustic stress corrosion cracking when designing components or systems that will be subjected to these conditions. This may involve the use of corrosion-resistant materials, protective coatings, and stress-relieving techniques to mitigate the risk of corrosion and cracking.
It is necessary to carefully monitor the condition of components and systems in high temperature and high pressure service to ensure that any issues are detected and addressed in a timely manner.
Caustic SCC Detection, Sizing and Monitoring Techniques:
WFMT, ACFM, and ECT can be effective techniques to detect these surface-breaking cracks.
Angle beam ultrasonic techniques (SWUT and PAUT) can be effective to detect, size cracks and periodically monitor crack growth.
Acoustic Emission Testing or AET can be used for locating cracks and monitoring crack growth in real time during operation.
Other techniques are also available and can be utilized for detection such as PT, MT and RT.
Watch below video created by CSB for a case study of catastrophic failure due to Caustic SCC of a pressure vessel manufactured from SA-723 Grade 2 a specification of "Alloy Steel Forgings for High-Strength Pressure Component Application", with maximum allowable working pressure (MAWP) of about 30,000 pounds per square inch gauge (psig) and maximum operating temperature of 750°F.
You can read the full investigation report in this link NDK Crystal Inc. Explosion with Offsite Fatality | CSB
Comments