Caustic Stress Corrosion Cracking-CSCC of Carbon Steel Weldments
- matintegrity
- Oct 10, 2021
- 3 min read
Updated: Jun 16, 2023
Corrosion by caustic (sodium or potassium hydroxide) at all concentrations is easily handled at room temperature with a variety of metals and alloys, including carbon steels. However, same materials with same operating conditions may become susceptible to Caustic Stress Corrosion Cracking, particularly under high applied or residual stress levels.
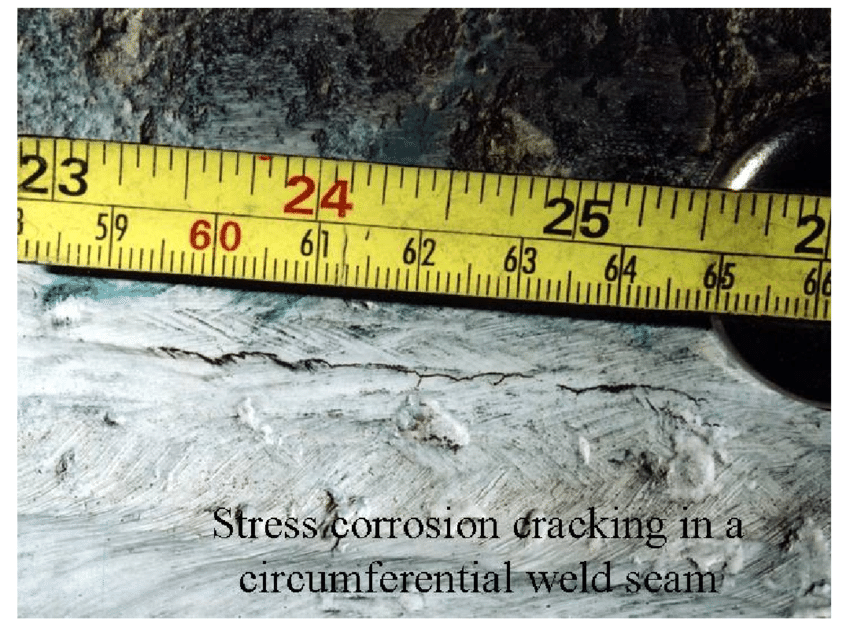
Caustic SCC is a form of Alkaline SCC and characterized by surface-initiated cracks that occur in piping and equipment exposed to caustic (alkaline hydroxide solutions) at elevated temperature, primarily adjacent to the as welded carbon steel welds.
The process equipment should be checked for caustic SCC, if the material known to be exposed to caustic solutions, particularly carbon steel. This type of attack is most likely to occur at connections for internal heating units and in areas of residual or other high stresses. The more susceptible areas are around nozzles and in or next to welded seams. Residual stresses generated from welding processes during equipment manufacturing, will lead to caustic SCC if not properly heat treated. Therefore, Cracking can be effectively prevented by means of a stress-relieving heat treatment. A heat treatment at 1150 °F (620 °C) minimum with a minimum holding time of 1 hr is considered an effective stress relieving heat treatment for carbon steel. The same requirement applies to repair welds and to internal and external attachment welds.
Remember: Caustic SCC occurs well below the critical corrosion parameters at which the caustic corrosion occurs. This means that cracking can occur at low caustic levels if a concentrating mechanism is present. In such cases, caustic concentrations of 50 ppm to 100 ppm may be sufficient to cause cracking.

Caustic SCC is characterized by surface-initiated cracks and mostly intergranular, but may become transgranular if contaminated with chlorides and/or cyanides. Caustic SCC typically propagates parallel to the weld in adjacent base metal, more likely in the zone of highest welding residual stresses, but can also occur in the weld deposit or HAZ and can be transverse to the weld. The pattern of cracking observed on the steel surface is sometimes described as a spider web of small cracks that often initiate at or interconnect with weld-related flaws that serve as local stress risers. Cracking that occurs in as- welded carbon steel typically appears as a network of very fine, oxide-filled cracks.
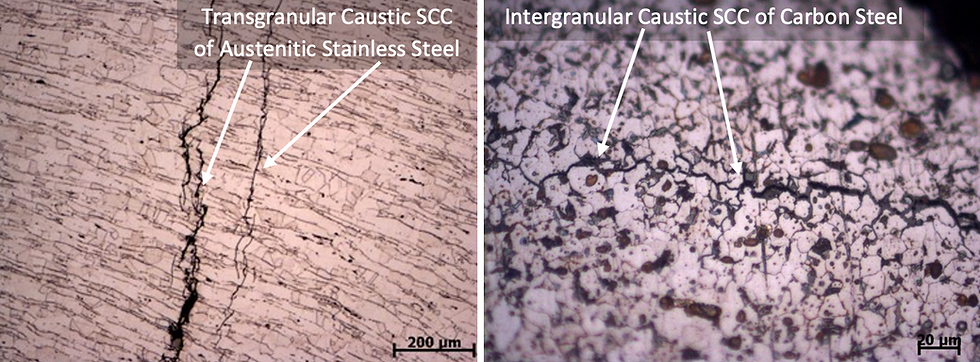
Metallographic examination when used, cracks would typically appears branched and predominantly intergranular. while cracking that occurs in as-welded or the non PWHT carbon steel typically appears as a network of very fine, oxide-filled cracks. In addition, visual inspection will disclose this type of attack especially when you see the caustic material seeping through the cracks and hence often deposit white salts that are readily visible.
Furthermore, the following examination methods can be effective for caustic SCC detection:
WFMT - Wet fluorescent magnetic test
ACFM - Alternating current field measurement
ECT - Eddy current test
Angle beam ultrasonic techniques (Shear Wave UT and Phased Array UT)
PT and MT (Dry or Wet)
Caustic SCC crack growth can be monitored by AET or Acoustic Emission Testing.
Need advise or Have a question
Do you have a problem in selecting the right materials? Do you need more information? please contact us or send your email and we will contact you.
Don not hesitate to share your thoughts in comments.
Kommentare