Flow Accelerated Corrosion (FAC) of Deaerator Tank
- matintegrity
- May 21, 2021
- 2 min read
A Deaerator (DA) Tank is a pressure vessel found in boiler systems, and used to remove gases (mainly oxygen) from condensate and make-up water. There are different designs available, however deaerator typically consists of a water storage section on the top and a deaerating or heating section on the bottom. The flow accelerated corrosion, is a common damage mechanism that occurs in deaerator systems and is caused by high local velocities and temperatures that maximize the corrosion rate.

One of the reasons for corrosion of boiler system components is dissolved gases such as oxygen, carbon dioxide, and ammonia in BFW, of which oxygen is the most important from a corrosion point of view. Make-up water contains considerable amounts of dissolved oxygen. The higher the amount of makeup water in the feedwater, the higher the amount of impurities and dissolved oxygen. Dissolved oxygen is the main cause of corrosion by oxygen pitting. It is a constant threat to the feedwater heater, economizer, and boiler tube integrity. Once dissolved oxygen is removed from the feedwater by using deaerators, the potential for corrosion drastically decreases.
The purpose of a deaerator is to reduce dissolved gases, particularly oxygen, to a low level and improve a plant's thermal efficiency by raising the water temperature. In addition, deaerators provide feedwater storage and proper suction conditions for boiler feedwater pumps. Deaeration process is done primarily by heating the feed water by low or High pressure steam to its saturation temperature when around 98% of dissolved gases separate from water and vent out.
Need advise or Have a question
Do you have a problem in selecting the right materials? Do you need more information? Whether you prefer to call through your company or as individual, please contact us or send your email and we will contact you.
The Deaerator's shell is typically made of carbon steel (CS), but the internals that come in contact with gases are of stainless steel, to withstand the corrosion due to operation severity (gases, temperature...etc.). However, deaerators also experience two-phase fluid flow. As fluid flashes upon entering a deaerator, oxygen departs with the steam. Thus, the water that impinges upon metal surfaces does not maintain an oxidizing environment. Furthermore, the pH of entrained water droplets within the steam is usually lower than the bulk water pH. The combination of these factors often initiates FAC in the deaerator.
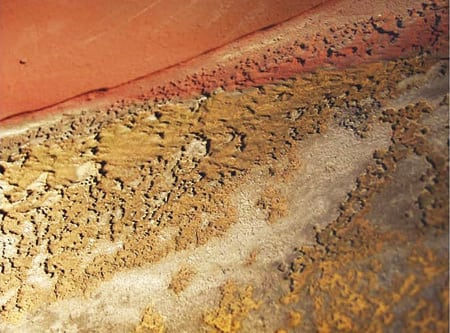
Corrosion protection in the boiler system is usually accomplished by laying down and continuously maintaining a layer of protective Fe3O4 (magnetite). However, if FAC is induced, the protective magnetite layer would be either dissolved or prevented from forming on carbon steel shell. Unlike carbon steel, low-alloy steel is more resistant to FAC due to containment of alloying elements, such as Cr, Cu, and Mo.
FAC failures are often located in areas where there is a flow disturbance and the wall thinning occurs just downstream of these flow disturbances leaving behind a corroded surface free of oxide scale, sometimes with a specific flow pattern.
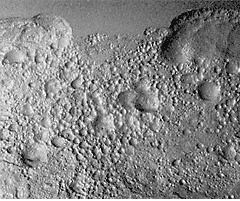
Don not hesitate to subscribe and share your comments.
Comments