Graphitic Corrosion of Cast Iron Pipes
- matintegrity
- May 4, 2023
- 3 min read
Graphitic corrosion, also known as graphite corrosion or selective leaching, is a type of corrosion that occurs in certain types of metals when they are exposed to aggressive environments. This type of corrosion is characterized by form of dealloying in which the iron matrix is corroded, leaving behind corrosion products and porous graphite. Graphitic corrosion can be a serious problem in certain applications, especially in the petrochemical, nuclear, and aerospace industries. In this article, we will discuss the causes, mechanisms, and prevention of graphitic corrosion.
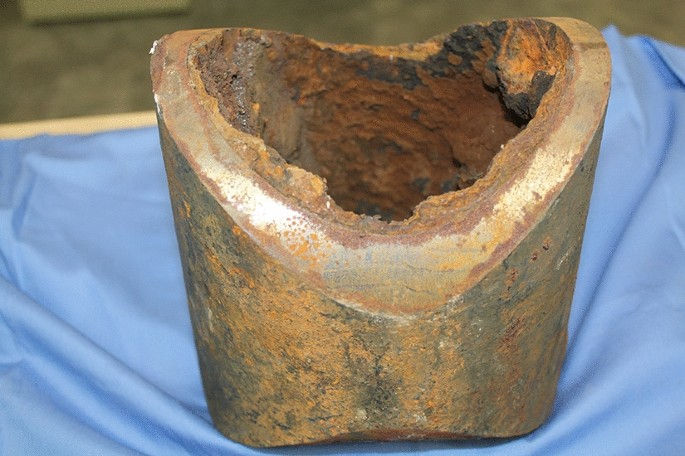
Attack results in a porous structure with a loss of strength, ductility, and density. It usually occurs under low pH and stagnant conditions, especially in contact with soils or waters high in sulphates.
Causes of Graphitic Corrosion
Graphitic corrosion occurs in metals that contain graphite particles or flakes, such as cast iron and ductile iron. These materials are commonly used in the petrochemical, nuclear, and aerospace industries due to their excellent mechanical properties and high resistance to wear and abrasion. However, they are susceptible to graphitic corrosion when exposed to certain aggressive environments, such as acidic or alkaline solutions, high-temperature water, and chloride-containing solutions.
The exact cause of graphitic corrosion is not fully understood, but it is believed to be related to the galvanic coupling between the graphite particles and the surrounding metal matrix. The graphite particles act as cathodes, while the metal matrix acts as anodes. This creates a localized corrosion cell, where the anodic metal is selectively removed, leaving behind a porous graphite skeleton.
Damage occurs in the presence of moisture or an aqueous phase, usually below 200 °F (95 °C).
Mechanisms of Graphitic Corrosion
The mechanism of graphitic corrosion is complex and depends on several factors, such as the composition of the alloy, the nature of the environment, and the temperature and pressure conditions.
In general, graphitic corrosion proceeds through the following stages:
Initiation: The corrosion process begins at localized defects in the metal surface, such as cracks, pits, or scratches. These defects create areas of high electrochemical activity, which accelerate the corrosion process.
Galvanic coupling: Once the corrosion process begins, galvanic coupling occurs between the graphite particles and the surrounding metal matrix. The graphite particles act as cathodes, while the metal matrix acts as anodes. This creates a localized corrosion cell, where the anodic metal is selectively removed, leaving behind a porous graphite skeleton.
Preferential leaching: As the corrosion process continues, the anodic metal is selectively leached from the alloy, leaving behind a porous graphite skeleton. This process is often referred to as selective leaching or preferential leaching, as it only affects one of the constituent metals in the alloy.
Corrosion product formation: As the anodic metal is removed, corrosion products may form on the metal surface, which can further accelerate the corrosion process. These corrosion products can also affect the mechanical properties of the alloy, leading to material degradation and failure.
Prevention of Graphitic Corrosion
Graphitic corrosion can be prevented by using appropriate corrosion-resistant materials and coatings, controlling the environmental conditions, and applying corrosion inhibitors.
Some of the effective prevention methods are:
Material selection: Choosing the appropriate material for a given application is critical to prevent graphitic corrosion. Materials that are resistant to the specific corrosive environment should be selected, such as stainless steel, nickel-based alloys, or titanium.
Coatings: Applying a protective coating to the metal surface can prevent direct contact between the metal and the corrosive environment, thus reducing the risk of graphitic corrosion. Coatings can be made of various materials, such as paint, plastic, or ceramic.
Environmental control: Controlling the environmental conditions, such as pH, temperature, and pressure, can also prevent graphitic corrosion. For example, reducing the acidity or alkalinity of a solution can reduce the corrosive potential.
Corrosion inhibitors: The use of corrosion inhibitors can also prevent graphitic corrosion. Corrosion inhibitors
References:
API RECOMMENDED PRACTICE 571 | Damage Mechanisms Affecting Fixed Equipment in the Refining Industry
Nishimura, T., & Okada, Y. (2015). Mechanism of Graphitic Corrosion in Cast Iron. ISIJ International, 55(6), 1211-1218. doi: 10.2355/isijinternational.55.1211
Kain, V., & John, A. T. (2017). Understanding the mechanism of graphitic corrosion in cast iron: A review. Materials Today: Proceedings, 4(8), 8206-8213. doi: 10.1016/j.matpr.2017.06.303
Dugstad, A., & Gjørv, O. E. (2017). Graphitic Corrosion in Cast Iron Pipes—A Review. Journal of Materials Engineering and Performance, 26(7), 3146-3162. doi: 10.1007/s11665-017-2678-1
Comments