Pressure Vessel Internal Inspection-Inspection of Nozzles
- matintegrity
- Oct 4, 2021
- 2 min read
The internal inspection shall be performed by a properly qualified inspector or personnel, and in accordance with the approved inspection plan. An internal inspection is conducted from inside the vessel and shall provide a thorough check of internal pressure boundary surfaces for damage. For internal inspections of too small vessels, manway or inspection port inspections can be substituted with remote visual inspection techniques.
Remember: pressure boundary is the portion of the pressure vessel that contains the pressure retaining elements joined or assembled into a pressure tight, fluid-containing vessel (e.g. typically the shell, heads, and nozzles), and excludes items such as supports, skirts, clips, etc. that do not retain pressure.
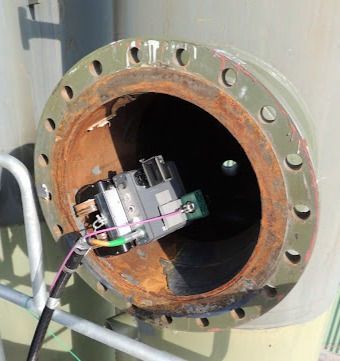
Typically, during on-stream inspection, the inspector shall be given sufficient access to all parts of the vessel (heads, shell, and nozzles) so that an accurate assessment of the vessel condition can be made. Consequently, the primary goal of the internal inspection is to find damage that cannot be found by regular monitoring of external Condition Monitoring Locations or CMLs that is performed during on-stream inspections.
Remember: CMLs may contain multiple examination points, for example, a vessel nozzle may be a CML and have multiple examination points (e.g. an examination point in all four quadrants of the CML on the nozzle).

Nozzle connection to shells are always considered as highly stressed areas and therefore they are susceptible to cracking. Whenever accessible, all nozzles should be internally inspected for corrosion, cracking, and distortion. The inspection can be visually conducted with the aid of a scraper and a flashlight and may include the following:
Exposed gasket surfaces should be checked for scoring and corrosion.
The surfaces should be cleaned thoroughly and carefully for a good visual inspection.
The grooves of ring-joint flanges should be checked for cracks due to excessive bolt tightening.
The stainless steel ring joint grooves should be checked for stress corrosion cracking.
NDE methods such as MT (wet or dry), PT, or UT shear-wave techniques may be used to supplement visual examination.
Lap joint flanges or slip flanges such as Van Stone flanges should be checked for corrosion between the flange and the pipe. The check can be made from inside the pipe by special probes and UT thickness-measuring devices.
Need advise or Have a question
Do you have a problem in selecting the right materials? Do you need more information? Whether you prefer to call through your company or as individual, please contact us or send your email and we will contact you.
Vessels in cyclic service (cycles of pressure, temperature, or combinations of both pressure and temperature) should be evaluated for potential fatigue cracking failures and have appropriate inspections planned. Special attention to nozzle reinforcing pads, longitudinal and circumferential weld joint peaking, repairs, modifications, and damage (e.g. dents, bulges, gouges, etc.), and their potential for fatigue cracking due to the stress intensification. An engineering analysis may be required to determine the high stress locations for further evaluation and inspection planning.
In addition, for shell and tube heat exchanger, the impingement baffle or plate that is placed below the shell inlet nozzle to prevent erosion damage of the tubes due to impingement of the incoming fluid, shall be visually checked and replaced if necessary.
Don not hesitate to subscribe and share your comments.
Comments