Steam Drum Failure Modes and Inspection Practices
- matintegrity
- May 29, 2023
- 4 min read
When considering the safe operation of boilers, various systems come to mind such as flame control, fuel/air ratio, steam pressure control, and vessel levels. However, one critical aspect often overlooked is the water within the boiler system. As steam is produced and utilized in processes, the condensate returns to the boiler as feedwater. Over time, this water becomes saturated with dissolved minerals and solids, potentially leading to various issues.
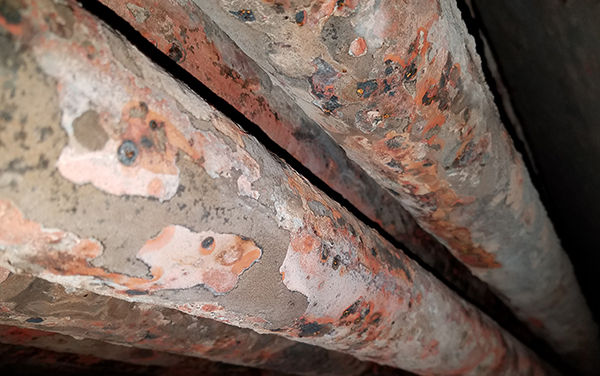
The Role of Boiler Blowdown
Boiler blowdown is the process of removing heavily saturated water from the system. It is essential to remove impurities accumulated in the water to ensure safe and efficient operation. During blowdown, the system water is replaced with fresh feedwater, which typically contains fewer impurities. By sampling and testing the system water, operators can determine the amount of dirty water that needs to be removed and accordingly add fresh feedwater to maintain the appropriate system water chemistry.
Types of Blowdown
There are two primary types of blowdown employed in modern boiler systems: bottom blowdown and surface blowdown.
Bottom Blowdown: This type of blowdown is carried out periodically and is usually performed from the mud drum of the boiler, where settled solids accumulate. Bottom blowdown can be automated or done manually.
Surface Blowdown: In larger systems, surface blowdown is performed continuously and is automated. In smaller systems, it may still be a manual procedure. Surface blowdown involves removing the system water from the steam drum, which typically contains the highest concentration of dissolved solids. The continuous stream exiting the drum usually passes through one of the water level controls before being discharged via a vent line. This process simultaneously removes impurity-laden water and prevents scale buildup in the level control legs.
Watch this video explain the recommended blowdown procedure.
Failure Modes Related to Water Level Control
Proper water level control is crucial in steam systems to prevent various failure modes. Insufficient water levels can lead to dry firing, where the tubes are exposed to the flame. This condition weakens the tube metal, increasing the risk of tube failure. On the other hand, excessively high water levels can result in water slugs entrained in the steam, leading to erosion and corrosion within the steam pipes.
Water Chemistry and System Integrity
Maintaining proper boiler water chemistry is vital for the safe and long-term operation of the boiler system. Below Figure illustrates the consequences of inadequate water chemistry control, showing the buildup of corrosive compounds or solid materials in the system. Pipes can suffer from corrosion, compromising their ability to withstand pressure differentials, or they can become clogged due to solids adhering to the inner walls.
Drums inspection practices:
Drums are a critical component of boilers, and their inspection is essential to ensure safe and reliable operation. The internal surfaces and connections of drums, including water-column connections and safety valve nozzles, should be thoroughly examined for various defects and issues. Deformation, corrosion, pitting, grooving, cracking, scale deposits, and sludge accumulation should be carefully inspected. Special attention should be given to seams, whether welded or riveted, as well as the areas adjacent to them.
Corrosion along or near seams is particularly critical and requires a close visual examination, along with ultrasonic wall thickness measurements. Grooving and cracks along longitudinal seams are of significant concern, as they usually occur under high stress conditions.
Poor water circulation areas are more susceptible to severe corrosion.
Both the internal and external surfaces of the drum should be examined, with the top external surface requiring cleaning to assess any corrosion.
To obtain a more comprehensive inspection of plate and weld metal for cracks and defects beyond visual examination, various methods can be employed as follows:
Radiography is effective for identifying cracks located below or near the metal surface.
Magnetic particle examinations, both dry powder and wet fluorescent, are useful for detecting cracks at or near the surface.
Ultrasonic tests using straight beam and shear wave techniques can indicate discontinuities at any depth, while dye penetrant tests are suitable for locating surface cracks.
Electromagnetic inspection techniques can also be employed for surface and sub-surface crack detection instead of magnetic particle and liquid penetrant examinations.
Crack connected to tube hole in the shell during visual examination of steam drum photo credit https://imgs.materials.life
Apart from the drum itself, the inspection should also cover the drum internals and connections. These include internal feed headers, distribution piping, steam separators, dry pipes, blowdown piping, deflector plates, and baffle plates.
Dry pipes, if present, should be inspected for deposits that may restrict flow, requiring the use of a hand mirror for indirect observation.
Additional inspection of drum appurtenances is necessary, particularly safety-valve nozzles and gauge-glass connections.
Accumulations of sludge or debris should be checked and visually inspected using a flashlight.
If the inside cannot be directly observed, a small hand mirror or specialized illuminating equipment may be used for indirect observation. Safety-valve nozzles and connections at the lower part of the drum should receive particular attention. Manhole davits should be tested for freedom of movement and excessive deformation, while manhole and handhole cover plates and nozzle seats should be examined for scoring.
Conclusion
When investigating boiler failures, it is crucial to examine not only the control systems directly associated with boiler operation but also the boiler blowdown and water chemistry control history and practices. Neglecting these aspects can lead to various issues, such as tube failures, erosion, corrosion, and clogged pipes. By implementing proper inspection practices, including regular blowdowns and monitoring water chemistry, operators can ensure the safe and efficient operation of boiler systems. Remember, steam is the lifeblood of many chemical plants, making it imperative to maintain the health and integrity of the system as a whole.
References:
American Petroleum Institute (API) RECOMMENDED PRACTICE 573 Inspection of Fired Boilers and Heaters
American Society of Mechanical Engineers (ASME). Boiler and Pressure Vessel Code, Section I: Rules for Construction of Power Boilers.
National Board of Boiler and Pressure Vessel Inspectors. Inspection of Fired Boilers and Heaters: Recommended Practices for the Inspection of Fired Boilers and Heaters.
Comments